we recognize the paramount importance of precision and quality in pharmaceutical manufacturing. Our AI-powered Visual Quality Inspection tool is engineered to meet the rigorous demands of the pharma industry, ensuring the highest standards of product safety and compliance. Utilizing cutting-edge AI technology, VIS delivers exceptional defect detection and quality assurance
Why VIS for Pharma Manufacturing?
Our solution utilizes advanced artificial intelligence to perform sophisticated visual inspections. The VIS system excels in identifying a wide range of defects that traditional methods might miss, including:
- Contaminants: Detects foreign particles and impurities in pharmaceutical products.
- Surface Defects: Identifies cracks, chips, and other imperfections in containers and packaging.
- Label Accuracy: Ensures labels are properly applied, correctly positioned, and free from errors.
- Dosage Verification: Confirms that tablets, capsules, and liquid medications are accurately dosed.
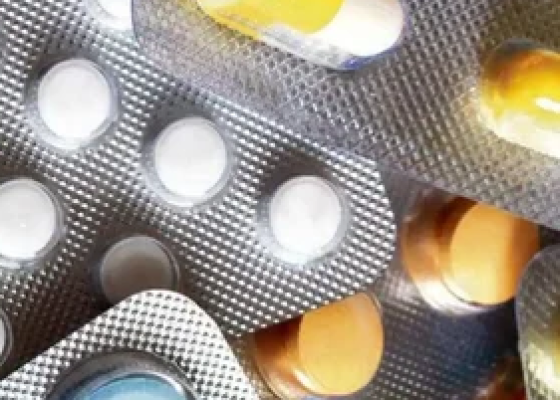
Types of Defect that VIS Can Detect through AI Based Image Processing Solution
Capsules
- Weight Variation: Significant differences in the weight of capsules, leading to dosage inconsistencies.
- Cap Separation: Caps and bodies of hard gelatin capsules separate easily.
- Filling Defects: Incomplete or uneven filling of the capsule contents.
- Appearance Defects: Discoloration, spots, or stains on the capsule surface.
- Cracking or Splitting: Capsules that crack or split during handling or storage.
- Gelatin Blooming: Uneven or mottled appearance due to improper drying of gelatin.
Tablets
- Weight Variation: Tablets with inconsistent weights leading to dosage inaccuracies.
- Friability: Tablets that easily crumble or break under pressure.
- Capping and Lamination: Separation of a tablet into layers.
- Chipping: Small pieces breaking away from the tablet edges.
- Sticking and Picking: Tablets sticking to the punch faces and being torn off during ejection.
- Mottling: Uneven color distribution on the tablet surface.
- Hardness Variation: Tablets that are either too hard or too soft.
Injections
- Particulate Matter: Presence of foreign particles in the solution.
- Color Variation: Discoloration or unusual coloration of the injection solution.
- Cloudiness: Cloudy or opaque appearance indicating contamination.
- Seal Integrity: Incomplete or broken seals on vials or ampoules.
- Volume Variation: Inconsistent volume of liquid in vials.
- Precipitation: Formation of solid particles in the solution over time.
Syrups
- Sedimentation: Settling of solid particles at the bottom of the bottle.
- Crystallization: Formation of crystals in the syrup.
- Color Change: Changes in color indicating possible degradation or contamination.
- Odor and Taste: Off odors or flavors that indicate spoilage or contamination.
- Microbial Contamination: Presence of bacteria, fungi, or other microorganisms.
- Viscosity Variation: Inconsistent thickness or flow properties.
Topical Creams and Ointments
- Phase Separation: Separation of the product into oil and water phases.
- Consistency Issues: Inconsistent texture, such as being too runny or too thick.
- Color Changes: Unusual discoloration indicating possible instability.
- Contamination: Presence of foreign particles or microorganisms.
- Packaging Defects: Leaking tubes, faulty seals, or damaged containers.
Eye Drops
- Particulate Matter: Presence of foreign particles in the solution.
- Cloudiness: Cloudy appearance indicating contamination.
- pH Variation: Deviations in pH affecting safety and efficacy.
- Sterility Issues: Microbial contamination compromising the sterility.
- Container Defects: Leaking or improperly sealed containers.
Powders
- Clumping: Formation of lumps or clumps due to moisture or improper handling.
- Inconsistent Particle Size: Variations in particle size affecting dissolution and absorption.
- Color Variation: Uneven color distribution indicating possible contamination or instability.
- Flowability Issues: Poor flow properties affecting packaging and dosing accuracy.
Transdermal Patches
- Adhesive Failure: Poor adhesive properties leading to the patch not sticking properly.
- Dose Uniformity: Inconsistent drug content across different patches.
- Physical Damage: Tears, cuts, or other physical damages to the patch.
- Packaging Defects: Faulty seals or damaged packaging compromising product integrity.
Key Features of VIS
High-Resolution Imaging
Equipped with high-resolution cameras, VIS captures detailed images of pharmaceutical products, ensuring no defect goes undetected.
Intelligent Machine Learning
Our machine learning algorithms continuously evolve, improving accuracy with each inspection cycle. This adaptive capability ensures the system remains effective against new and evolving defect types.
Customizable Parameters
VIS allows customization of inspection parameters to match the specific needs of your production line, whether for tablets, capsules, injectables, or other forms.
Comprehensive Analytics
VIS provides in-depth analytics, helping you track defect trends, identify root causes, and implement proactive quality improvements
Benefits of Vision Intelligence System for Pharma
Enhanced Product Safety
VIS ensures that every product meets the highest quality standards, protecting patient safety and ensuring regulatory compliance.
Increased Efficiency
By automating the inspection process, VIS reduces the need for manual inspections, minimizing human error and increasing overall efficiency.
Cost Reduction
Early defect detection with VIS helps prevent costly recalls and reduce waste, leading to significant cost savings.
Scalability
VIS is designed to scale with your business, providing robust inspection capabilities whether you are a small manufacturer or a large pharmaceutical enterprise.