In Retail & FMCG Manufacturing, visual quality inspection is essential for ensuring that products meet regulatory requirements, such as those related to food safety and labeling. By analyzing product labels and packaging, visual inspection systems can identify any discrepancies or errors that could lead to non-compliance with regulations. This can help manufacturers avoid costly recalls and protect their brand reputation.
Vision Intelligence System for Retail and FMCG Industry
No need to check every dimension and detail manually, switch your technology to intelligent quality detection, check the structural quality, dimensional accuracy, and operations quality in just a matter of seconds. Assure accurate ingredients and up-to-the-mark quality. As soon as you let automatic detection in, even particles that are hard to be found from naked eyes are spotted. Detect any foreign particles like metal, insects, unwanted ingredients, dirt, wood, small animals, and thorns. Make sure the color is accurate and your product looks perfect.

Packaging defects
Visual inspection systems can detect packaging defects such as cracks, dents, or tears that could compromise the integrity of the product.
Color variation
Consistency in color is important for maintaining brand identity and visual appeal. Visual inspection systems can detect color variations in products, packaging, or labels that may indicate a problem in the manufacturing process.
Labeling defects
Incorrect or missing labels can lead to non-compliance with regulations and legal issues. Visual inspection systems can identify missing or incorrect labels, as well as any discrepancies between the label and the product inside.
Size and shape defects
Products that do not meet size or shape requirements can be difficult to package or display, leading to increased costs and decreased efficiency. Visual inspection systems can detect size and shape defects and ensure that products meet the required specifications.
Contamination
FMCG products such as food and beverages can be contaminated during the manufacturing process, which can lead to safety issues and product recalls. Visual inspection systems can detect contamination such as foreign objects, bacteria, or mold.
Texture and appearance defects
FMCG products should have a consistent texture and appearance. Visual inspection systems can detect defects such as uneven texture, discoloration, or other visual imperfections that could affect product quality and consumer perception.
Types of Defect that VIS Can Detect through AI Based Image Processing Solution
Packaging Defects
Misaligned Labels
- Description: Labels that are crooked or improperly placed on the packaging.
- Impact: Misaligned labels can lead to poor shelf presentation and potential regulatory issues.
Broken Seals
- Description: Seals that are damaged, incomplete, or tampered with.
- Impact: Compromised seals can lead to contamination and reduced product shelf life.
Damaged Packaging
- Description: Tears, dents, holes, or other physical damage to the packaging materials.
- Impact: Damaged packaging can result in product contamination, spillage, and customer dissatisfaction.
Incorrect Information
- Description: Errors in printed information such as expiry dates, batch numbers, or ingredient lists.
- Impact: Incorrect information can lead to regulatory non-compliance and potential health risks for consumers.
Product Defects
Cracks and Chips
- Description: Physical damage to the product, such as cracked bottles or chipped containers.
- Impact: Cracks and chips can compromise product integrity and safety.
Foreign Particles
- Description: Presence of contaminants or foreign particles within the product or packaging.
- Impact: Contaminants can pose serious health risks and lead to product recalls.
Inconsistent Fill Levels
- Description: Variations in the amount of product filled in each package.
- Impact: Inconsistent fill levels can result in customer complaints and potential regulatory issues.
Color Variations
- Description: Inconsistencies in product color that indicate potential quality issues.
- Impact: Color variations can signal production issues or product degradation.
Labeling Defects
Smudges and Misprints
- Description: Blurred, smeared, or incomplete printing on labels.
- Impact: Smudged or misprinted labels can render important information unreadable, leading to compliance issues.
Missing Labels
- Description: Products that lack the necessary labeling.
- Impact: Missing labels can result in regulatory non-compliance and customer dissatisfaction.
Incorrect Placement
- Description: Labels placed incorrectly, such as over seals or in the wrong position on the packaging.
- Impact: Incorrect label placement can hinder readability and affect product presentation.
Content Consistency
Clumping or Separation
- Description: Issues with product texture or uniformity, such as clumped powders or separated liquids.
- Impact: Clumping or separation can indicate improper formulation or storage conditions, affecting product performance.
Weight Variation
- Description: Significant differences in product weight across different units.
- Impact: Weight variation can lead to customer complaints and regulatory non-compliance.
Shape and Size Irregularities
- Description: Deviations in the expected shape or size of the product.
- Impact: Irregular shapes or sizes can affect product usability and consumer perception.
Additional Defects
Surface Defects
- Description: Scratches, dents, or other surface imperfections on the product or packaging.
- Impact: Surface defects can impact the visual appeal and perceived quality of the product.
Barcode Issues
- Description: Barcodes that are missing, misprinted, or unreadable.
- Impact: Barcode issues can disrupt inventory management and sales processes.
Seal Integrity
- Description: Seals that are improperly applied or do not maintain integrity.
- Impact: Compromised seal integrity can lead to leakage and contamination.
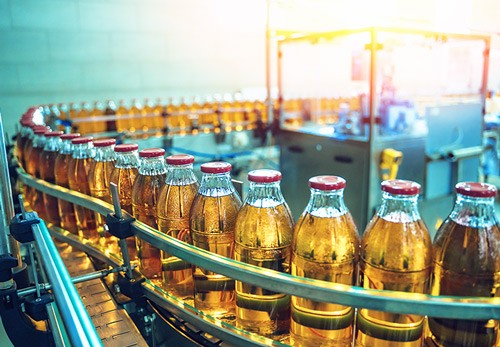
Benefits of Trident's Vision Intelligence System for Retail & FMCG Manufcaturing
- Improved product quality: Visual quality inspection ensures that products meet the required standards, resulting in improved product quality and consistency. This helps to maintain customer satisfaction and can increase brand loyalty.
- Increased efficiency: By detecting defects early in the manufacturing process, visual inspection systems can help to reduce waste, improve production efficiency, and lower costs.
- Compliance with regulations: Visual inspection systems can ensure that products meet regulatory requirements and prevent costly product recalls or legal issues.
- Enhanced brand reputation: By ensuring that products are visually appealing and free from defects, visual quality inspection can enhance brand reputation and increase customer trust.
- Better inventory management: Visual inspection systems can scan barcodes and product labels to ensure that the correct products are in the correct locations. This helps to prevent out-of-stock situations and reduces the time it takes to restock shelves.
- Faster time to market: Visual quality inspection helps to detect defects early in the manufacturing process, reducing the time it takes to address and correct issues. This allows products to be brought to market faster, increasing competitiveness and profitability.