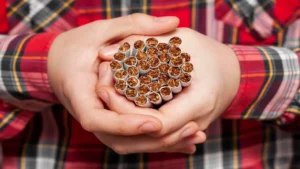
Visual Quality Inspection – Trident's Vision Intelligence System
Our Vision Intelligence System provides you surplus confidence that your products are free from defects and discontinuities as we use the industry’s most considered and recognised standards and processes to closely and carefully inspect your products, no matter how big or how large the quantity.
Among the many enterprises where visual inspecting is needed, there are several area where visual inspecting is considered to be of very significant and is a top priority activity due to the potentially high cost of any mistakes that may occur during inspection such as accident, fatality, failure of specialized equipment, scrapped products, rework, or a loss of customers. These areas of visual inspection also cover food industry, pharmacy, and medication
Why not just stick to manual inspection?
There are several limitations to using the old traditional way of inspection. Manual inspecting needs the presence of a person, an investigator who conducts an evaluation of the object under inquiry and gives a report on it according to some training or previous knowledge. No tools are needed to inspect except the naked eye of the trained investigator.
Research says visual inspection errors typically vary from 20% to 30%. Some defects can be attributed to human mistakes, while others are due to space constraints. Some errors can be overcome through training and practice, but cannot be eliminated completely.
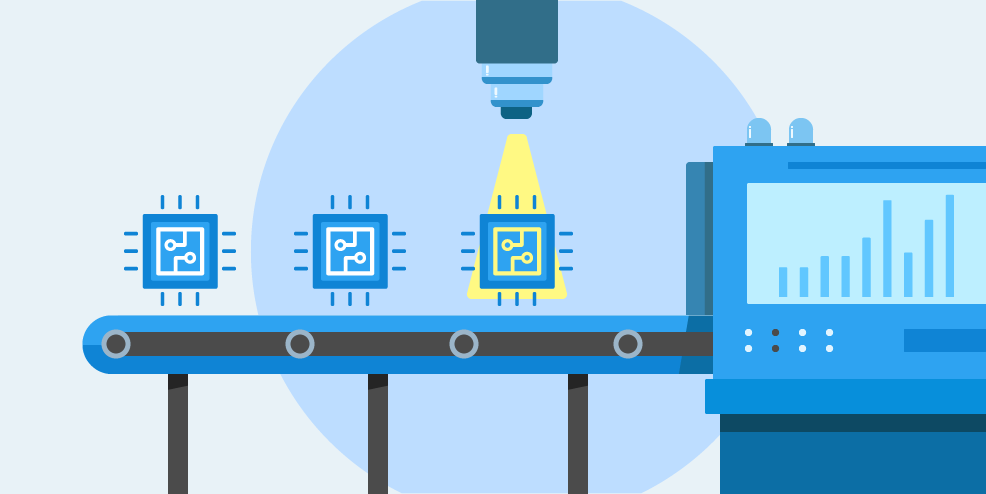
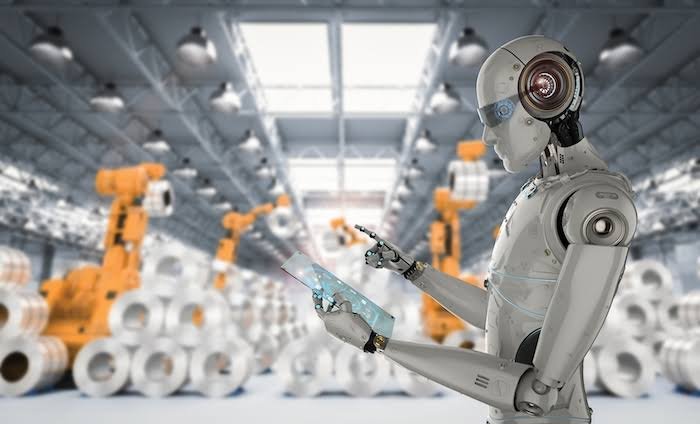
Why Vision Intelligence System Platform?
Among the many enterprises where visual inspecting is needed, there are several area where visual inspecting is considered to be of very significant and is a top priority activity due to the potentially high cost of any mistakes that may occur during inspection such as accident, fatality, failure of specialized equipment, scrapped products, rework, or a loss of customers. These areas of visual inspection also cover food industry, pharmacy, and medication.
Transform Manufacturing Quality unit into prompt-return centre
Our platform is developed to convert the quality unit of manufacturing companies into profit-inducing centres. We have achieved this by minimising manufacturing defects to the barest minimum, implementing corrective and preventing processes, satisfying customer experience and providing the support manufacturers need to comply with international compliance standards.
Backbone of Trident's Vision Intelligence System
- Install guidebook for manufacturing process and VQI will follow those parameters.
- Define various kind of defects, to get identified by camera overhead production line.
- Get alerts when any defect is captured in the camera
- Get alert as per your choice: Dashboard or Mobile App
- Integrate IoT devices such as cameras and scales to let operators check if output is within parameters
- Get real-time data to enhance visibility into process
Value to customer
- Value of implementing Trident’s Vision Intelligence System platform is that the inspection process can provide valuable manufacturing intelligence that can then be used to design better quality products and processes. Every continuous improvement program is reliant upon gathering data to improve efficiency.
- It provide insights into how a better design might lead to higher quality and less waste. Statistical Process Control (SPC) analyses can be performed on inspection results to gain insights for process improvement along your entire production process.
- Quality Inspections can help to reduce future costs, including rejected or returned items (perhaps damaged during shipment based on a packaging defect), higher warranty returns or more calls into your customer support centre
Our Promise to you
Adopting this platform will be a boon by:
- Interpret defects and solved before forthcoming delay
- Boost first output by locating and solving the root cause of quality defects.
- Widen quality by permit fixer to outline defective parts.
- Save time by digitizing the defect-reporting activity.
Tangible Benefits/Desired Outcome
- Optimize to major cost-product and manpower
- Sampling of product inspection can be eliminated due to continuous inspection through vision cameras
- Can revise all the defected products from data storage
- Root cause analysis of defection can be done on real time basis
Case Study from Leading Manufacturing Industry
“We needed continuous inspection of each packet which can run between 300-600 packets per minute over conveyor belt, as currently inspection is done after every 30 minutes and it can tend to manufacture 9000-18000 defected packets per minute which is a surplus loss. After on boarding to Visual Quality Inspection this rate has been decreased as any wrong/defected product inspected by camera gives an alert to the human inspector on real time basis”.